高速加工中心是一种集机械加工、控制系统、自动化及高效装夹技术于一体的现代化数控设备。以较高的主轴转速和进给速度,适应于轻金属和塑料等材料的高效切削,加工精度高,适用于模具制造、航空航天、汽车等制造产业。通常指主轴转速在8000rpm以上的数控加工设备,其高速度的特点使得加工过程更为高效、精准,同时也能够保证良好的表面质量。它能够执行多种加工工艺,包括铣削、钻孔、攻丝、切割等,适用于不同形状和材料的工件。
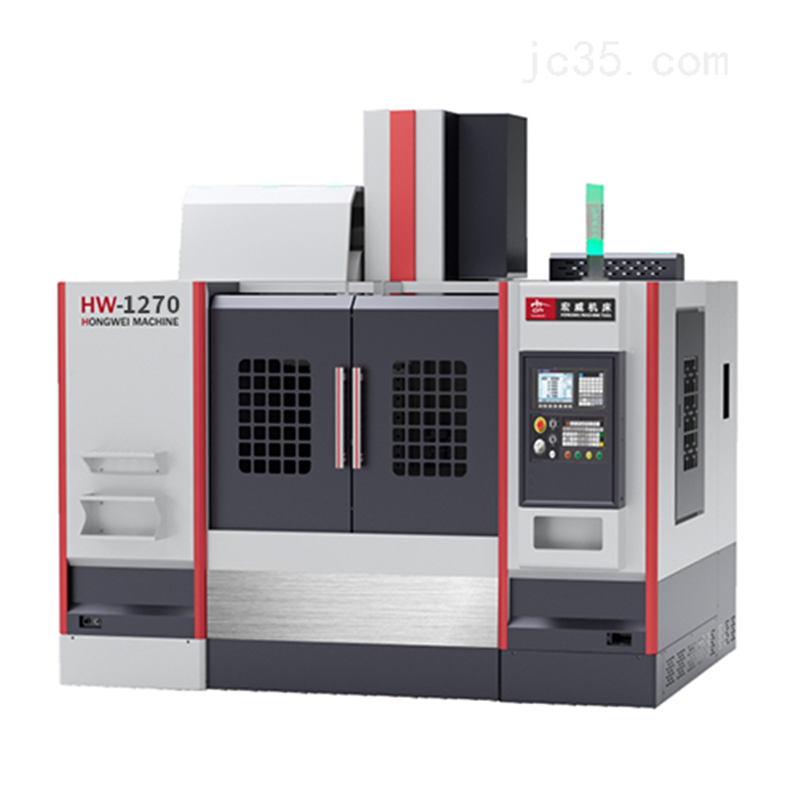
1.预热阶段:在正式加工之前,设备通常需要进行预热,以达到稳定的操作状态,防止热变形影响加工精度。
2.刀具选择与安装:根据加工工艺要求,系统自动选择合适刀具,并进行快速换刀。
3.加工过程:加工中心根据预设的程序,自动执行各种切削动作,控制主轴转速、进给速度、刀具路径等,完成对工件的加工。高速加工的特点在于快速的进给和切削,通常能够达到更高的加工效率。
4.冷却与润滑:在加工过程中,冷却液通过冷却喷嘴喷入刀具和工件接触区,有效降低切削温度,延长刀具寿命。同时,冷却液能够带走切屑,保持切削区域的畅通。
5.加工完成:加工完成后,系统自动进行清洁和检查,确保质量符合标准。
优点:
1.加工效率高:由于高主轴转速和高进给速率,使得加工过程中的切削时间大大缩短,提升了整体加工效率。
2.切削精度高:其刚性和稳定性极大减小了切削过程中的振动,提高了加工精度,能够满足高精度零件加工的需求。
3.表面质量好:高速切削减少了刀具与工件的接触时间,降低了表面粗糙度,提升了加工后工件的表面质量。
4.适应性强:能够加工多种材料,包括铝合金、工程塑料等轻质材料,以及在某些条件下的硬质合金。
5.加工灵活性高:能够快速实现不同产品的切换,适应小批量、高精度加工的需求,适合多品种小批量生产。
选择高速加工中心的考虑因素:
1.加工类型与材料:根据实际的加工需求,选择适用于特定材料和加工类型的加工中心。
2.主轴转速与功率:主轴的转速和功率直接影响切削能力和效率,具体需求应根据加工的材料和部件来确定。
3.行程范围:考虑加工部件的尺寸,选择合适的行程范围,以确保能满足各类产品的生产需求。
4.控制系统:现代数控系统的功能和易用性各异,选择功能完善、操作简便的控制系统能提高生产效率。
5.刀具及自动换刀系统:检查刀库的容量和换刀系统的速度,选择能合理匹配生产工艺的刀具和换刀方案。
6.售后服务:设备采购后的维护和技术支持同样重要,应选择提供良好售后服务和技术支持的供应商。