高速加工中心是一种高效的加工设备,广泛应用于机械制造、航空航天、汽车工业、模具制造及精密加工等领域。与传统加工设备相比,特点是加工速度快、精度高、自动化程度高,对于复杂零件的生产具有显著优势。利用高速主轴和高进给率的特点,通过精密的控制系统,完成对工件的切削、铣削、钻孔等多种加工操作。工作时,主轴以高的速度旋转,配合高效的刀具和切削液,使材料在短时间内去除,达到快速成型的目的。
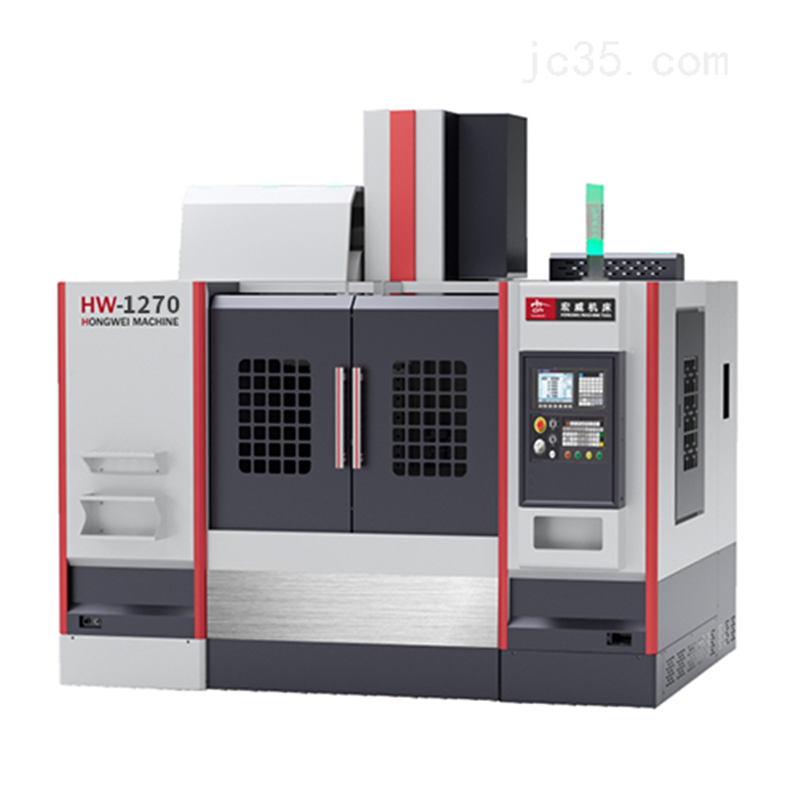
高速加工中心的组成:
1.机床基础:机床的基础框架,提供稳定性和减震性能,确保加工精度。
2.主轴部件:负责刀具的旋转,通常采用高精度的滚珠轴承,确保平稳运行。
3.刀具交换系统:配备自动换刀装置,能够快速更换刀具,缩短非加工时间,提高效率。
4.工作台:用于固定工件,通常采用T型槽设计,让操作员方便夹持和定位工件。
5.数控系统:通过控制面板和软件,输入加工程序,精准控制机床各部分的运动。
6.传动系统:由电机驱动的传动装置,精确控制各轴的移动。
应用领域:
1.模具制造:能够高效加工复杂的模具形状,满足关于模具产品对精度和光洁度的要求。
2.汽车工业:在发动机及其部件的加工中,能够快速且精准地完成零部件的生产。
3.航空航天:对轻质材料和复杂曲面的加工需求,在航空航天领域得到广泛应用。
4.医疗设备:医疗设备的精密部件需要高精度的加工,能够达到理想效果。
5.电子产品:在消费电子、通讯设备等产品的制造中,要求高效率和高精度的零部件,速度加工中心能够满足这些要求。
高速加工中心的操作流程:
1.程序编制:根据工件图纸,使用CAD/CAM软件编制加工程序。
2.机床准备:检查机床的各项系统,包括主轴、冷却系统、刀具等,确保设备正常工作。
3.工件夹持:将待加工的工件固定在工作台上,确保夹紧稳固,不易移动。
4.刀具选择:根据加工要求选择合适的刀具,并安装到主轴上。
5.输入程序:将加工程序上传至数控系统,设置相关参数,如切削速度、进给率等。
6.开始加工:启动机床,监控加工过程,确保切削稳定。
7.后处理:加工完成后,取下工件,对表面进行后处理(如去毛刺、清洗等)。